1、Sintering Flue Gas Circulating Technology-Energy Conservation, Consumption Reduction, Pollution Minimizing and Efficiency Enhancement
Flue gas circulating technology is a cleaner production technology developed based on the theory that part of hot flue gas is brought back into sintering process. The flue gas circulating technology devised by NETC is applicable to varieties of processes and by the source of circulating flue gas, this technology is mainly divided into two modes: internal circulation and external circulation.
Effects of Energy Conservation and Emission Reduction
Reducing 20% to 50% of total emitted sintering flue gas is the most effective method to alleviate flue gas pollution in sintering plant.
Reducing emission of hazardous substances per unit product
Significantly reducing investment and operating cost of sintering flue gas treatment facilities (including hazardous substance removal device)
Sintering hot flue gas circulation: increasing thermal utilization and reducing 2% of solid fuel consumption
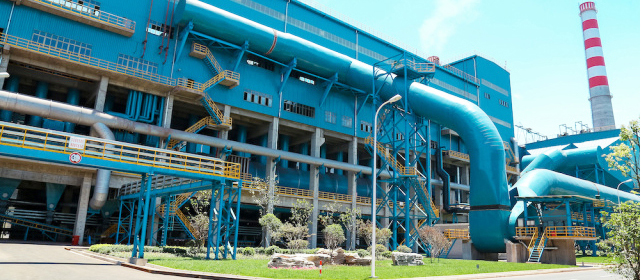
2、Flue Gas Purification Technology with Active Coke Five in One, Collaborative Treatment, Proprietary Intellectual Property Right and Domestic Equipment: Saving about 50% of Investment
For flue gas purification technology with active coke, coal-based active coke is used as absorber to absorb and remove SO₂ in flue gas. Active coke after absorption can be reclaimed by heating and the desorbed gas mixture containing high-density SO₂ can be directly used to produce 98% concentrated sulphuric acid, achieving recycling of sulphur. Meanwhile, catalytic function of active coke is used to reduce NOx in flue gas to N₂ and water by adding proper amount of ammonia, and thus efficiency of desulphurization can reach above 98% and efficiency of denitration can reach 70%. In addition, this technology has good results of removing heavy metal and dioxin in flue gas. No waste water or waste residue is generated in the process of purification and it’s an advanced flue gas purification technology that completely solves environmental problems in steel and iron industry.
Energy Conservation and Emission Reduction Effects
Desulfurization, denitration, dioxin removal, heavy metal removal and dedusting are achieved at one stroke with desulfurization rate above 98% and denitration rate of 70%.
Dry processing with no waste water or waste residue generated in the process of purification and with no secondary pollution
Low corrosion on equipment and low maintenance cost
Reclamation of by-product, which is 98% concentrated sulfuric acid and has goof economic returns
It can be used in cooperation with sintering process to dispose(slake) of desulfurized fly ash produced by calcium-based semi-dry desulfurization process and at the same time, the yield of by-product, sulfuric acid can be improved and returns can be increased.
3、Technology for Efficient Recovery and Utilization of Waste Heat Resources of Circular Cooler—Distinguished sealing technology: Ensuring Efficient Recovery and Gradient Utilization of Waste Heat
A multi-functional high-efficient sintering circular cooler and waste heat gradient and efficient utilization technology:
It can be applied to fabrication of new equipment and also for renovation of traditional sintering circular cooler. Through such measures as adjusting cooling air
flow and material bed thickness, lowering air leakage of sintering system and cooling system, waste heat gradient utilization technology can achieve efficient recovery of sensible heats of sinter ore product and sintering flue gas and gradient utilization of recycled waste heat.
Energy Conservation and Emission Reduction Effects
(1)Multi-functional High-efficiency Sintering Circular Cooler
No.
|
Name
Content
|
Traditional circular cooler
|
Multi-functional high-efficiency circular cooler
|
1
|
Main sealing technology
|
Dynamic seal
|
Mechanical seal, liquid seal or granulate media seal
|
2
|
Sealing material
|
Rubber seal
|
Heat-resistant seal, liquid or granulate media
|
3
|
Power consumption of cooling fan
|
7.5kilowatt /t-s
|
5.5kilowatt/t-s
|
4
|
Air leakage rate
|
30~50%
|
Below 5%
|
5
|
Pallet car structure
|
Single-deck pallet car
|
Welding fan-shaped pallet car structure with removable grate plates
|
6
|
articulated beam structure
|
Triangle beam
|
articulated beam structure with annular section
|
7
|
waste heat power generating amount
|
18~22kW·h/t-s
|
20~25kW·h/t-s
|
8
|
Equipment maintenance freqency
|
High
|
Low
|
9
|
Site environment
|
Poor
|
Good
|
(2) Waste Heat Gradient and Efficient Utilization Technology
Reducing energy consumption for sintering process by 3 to 5 kgce/t-s
Dust-suppression pipe waste heat utilization technology is adopted as well and power generation can be increased by 2 kW.h to 5 kW·h for finished product ore per ton.
4、Integrated type Environment-friendly Screening System—Vertical Sizing Process with High Efficiency, Low Energy Consumption & Emission and Small Occupation of Land
Integrated type environment-friendly screening system is developed jointly by NETC and Ji'nan Zhongran Technology Development Co., Ltd. Vertical arrangement is possible with equipment in small size, saving occupation of land; bar type mesh and a fully-enclosed structure are adopted for vibrating screen and only tiny negative pressure is required inside to satisfy dedusting requirements, greatly reducing the pressure of dedusting system; Vibrating equipment is light-weighted equipped with a mall power motor, saving electric energy.
Energy Conservation and Emission Reduction Effects
For 360㎡ sintering machine, comparison between traditional screening system and integrated type screening system in terms of investment and operation cost are as follows:
Name of system
Item
|
Traditional screening system
|
Integral type environment-friendly screening system
|
Qty
|
comparison with traditional screening system
|
1.Investment of process equipment
|
0.6 Million RMB/set
|
0.3 million/set
|
6 sets
|
Saving 1.8 million Yuan RMB
|
2.Electricity saved during operation of process equipment
|
90kW/set
|
15kW/set
|
6 sets
|
Saving 2.84 million Yuan RMB per year
|
3.Electricity saved during operation of dedusting system
|
1450kW/set
|
360kW/set
|
1 set
|
Saving 6.89 million Yuan RMB per year
|
By comprehensive comparison, for 360m2 sintering project, application of sizing system can save 9.73 million Yuan/a approximately in capital consumption of electric power .
|
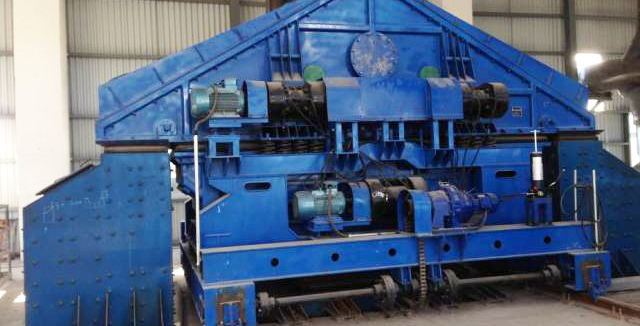
5、Sintering Optimization System—realizes simulation of sintering process and control by artificial intelligence expert Sintering optimization system is a control system based on sintering process model with intelligence expert system as control core. This system inputs operating experience and habits of process operation experts into knowledge base of expert system and uses them as basis for expert system to guide production. The system mainly contains three parts, which are process information and data management system, process model and sintering expert system.
Compared with conventional process control, process operation is more smooth and steadier. Monitoring of measured data and process guidance based on this measured data become more efficient.
Energy Conservation and Emission Reduction Effects
Reducing fuel consumption: Coke consumption for sinter ore per ton decreases by 1 to 2 kg
Stabilizing product quality: Avoiding major control acts and critical process conditions, for example, standard deviation of basicity fluctuation drops by 3% to 5%.
Improving productivity: 4% to 5%
Properly reducing emission
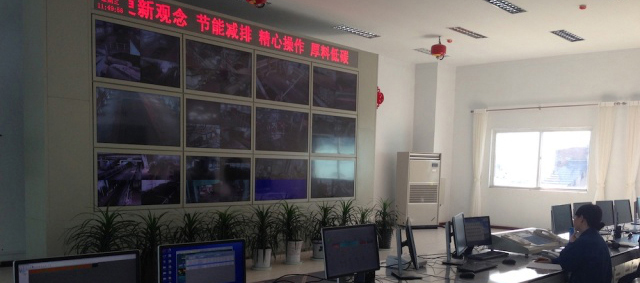
6、High-efficiency Sintering and Dedusting Technology—high dedusting efficiency,strong stability and compliant with the latest emission standards
High-efficiency sintering and dedusting technology is a main technological means to control and handle fine particulate and dust nowadays, characterized by high efficiency, strong stability, low resistance of filter bag, long service life and lesser maintenance. Equilibrium simulation technology for dedusting pipe network can reduce unbalance of pipe networks, make the most of effective air flow do dedusting, save investment in the system and reduce operation cost. Dedusting system adopts the most advanced wear-resisting technology, which significantly reduce the wear of dedusting pipe network, lower operation cost and decrease labor intensity of maintenance.
Energy Conservation and Emission Reduction Effects
Reducing emission load of hazardous substance per unit product and keeping dust emission concentration no more than 20mg/Nm³ on a stable and long-term basis;
Low operating resistance: Power of induced draft fan with 10000 m³/h flow rate can decrease by 1.74kW;
High dedusting efficiency: Dedusting efficiency at electrical area is 75% to 80%;
Long dedusting cycle: Its dedusting cycle is 3 times longer than mere bag filters;
Low consumption of air: Consumption of compressed air is lower than 1/3 of mere bag filters.
Long service life of filter bag: service life of filter bags can extend 1year more than mere bag filters.
Low comprehensive operation and maintenance fees for equipment
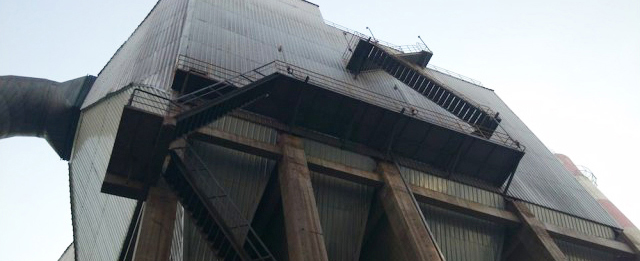